The art of migration – Open heart surgery while running a marathon: Exchange mission-critical processes and IT systems while continuing to successfully execute manufacturing operations without disruption. Migrations may be designed and performed either as a knife-edge roll or as systematically designed iterations, or a combination of both. Successful migrations ensure legacy processes and systems may be cumulatively decommissioned, without disruption to operations, data integrity or the enterprise.
How to support challenges of tightly knit operations?
One major motivation for considering state-of-the-art solutions is, of course, enabling features that many new manufacturing IT solutions provide off-the-shelf.
Analyzing the mix of vendors, applications, and developing the necessary migration and deployment strategies is time consuming, and error prone. Having spent 30 years successfully integrating many of the leading manufacturing software solutions, we have an established track record of providing best in class consulting services in the field of licensing third party manufacturing software and related IT solutions. Our team of expert consultants is uniquely positioned to help you analyze, select and license software to enable digital manufacturing.
- How do MES and other manufacturing control applications sync with each other and your ERP?
- How can you, for example, lock expired consumables in real-time to prevent their use in manufactured products, reduce waste, increase yield and focus on value-add activities?
- How do your sites efficiently exchange data to act as a fine-meshed manufacturing network?
- How do you track your devices and components through various sites all over the world or at your next-tier supplier?
How do you migrate to a service-based or message-oriented IT architecture? One that allows software modules distributed over heterogeneous platforms and reduces the effort and complexity of maintaining and developing multiple interfaces, operating systems, and communication protocols?
When considering a migration, it is imperative that you select a partner that can adequately address these questions. Setting up a quick pilot project is easy, but for enterprise-wide deployment there are strategic end-to-end considerations.
For example, some seriously undervalue, and thus miss, the opportunity to drive unification and interoperability through application-aligning activities such as incorporating master data management into new software rollouts.
Solutions like SAP Manufacturing provide built-in data synchronization with the ERP and other systems, with no need to import or export, manually maintain, map or normalize data from any silos.
Why migrate to a new manufacturing IT solution?
Manufacturing IT solutions are the operational hub of your manufacturing processes and, once again, you’ve been tasked with extending a system’s core capabilities in order to capture new market share. The existing MES system is written in COBOL, or another legacy language, and the lead developer is planning to retire soon.
To further complicate matters, you are facing the prospect of buying hardware for your SPC and Engineering Data Collection system on ebay. And the domain experts responsible for implementing the business logic in your Dispatching system are now managing factories in a remote location.
And your new-hire, computer science and industrial engineering teams were trained in systems that are far more current and advanced than those running in your factory.
Many customers face some or all of these issues. For all of the new IT manufacturing solutions on the market, few product vendors are willing or able to discuss in coherent detail how they will get you there.
That is, how they will provide the support you need to migrate from solution A to solution B; much like open heart surgery, the process to migrate an operational system is difficult and requires deep expertise and skill.
MES migration scenarios
The MES is the central hub of manufacturing operations. Regardless of whether it is a legacy, COBOL-based solution or a custom-developed one, the MES encapsulates your manufacturing runtime processes.
While there may be limitations in the existing system, the first step in a migration is to document the as-is system in order to ensure a thorough understanding as to how the current system is utilized. Next, the as-is manufacturing landscape, business goals and priorities are developed into a conceptual blueprint to determine which components will be replaced, which reused, and which decommissioned.
The blueprint is further elaborated, resulting finally in the to-be solution. Finally, a migration strategy and project plan are developed to define the process to move from the as-is to to-be. Easy to imagine, difficult to achieve, and even harder to realize.
Consider the migration of the production system. There are several ways to approach this, and most likely a hybrid approach will be planned that balances the goals and risks of the project.
Knife-Edge-Roll
- Switch off old application
- Migrate data
- Switch on new application
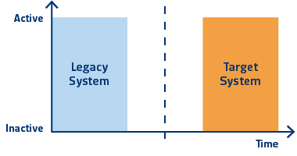
Parallel Operation
- Old application used as operative application
- New applicaion used (non-operative) in parallel
- Set new application into operation
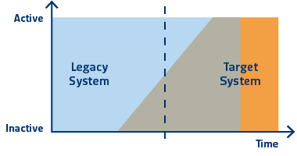
Function by Function
- Run old application
- Substitute function by function with new system
- When all functions are substituted, switch old system off
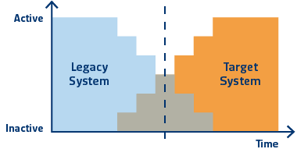
New Production Starts
- Run old application
- Build and establish new system and start new lots on it
- After all production orders are in the new system, switch off the old system
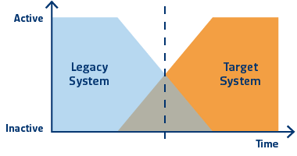
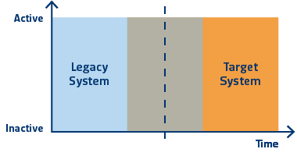
In the planning phases, the team should consider the operational aspects (R&D vs. high-volume production, number of products, planned shutdown windows, high vs. low integration of equipment, applications, etc.).
The migration will require support from the highest levels of the organization and is at risk of failure if not supported by the operations teams. To execute a complex migration of a running system requires experience and skilled attention to ensure the running operations are not seriously impacted and that, upon completion, the factory is positioned to truly capitalize on the promised benefits of the new solution.