Thomas Lang, on November 06, 2018, 08:45 AM
Carrier and Material Tracking in Production
Once again you cannot find material in your production facility and St. Anthony is out on holiday? Not to worry … technology will save the day! With the widespread adoption of digital tracking systems over the past few years, they’ve become more economical. But which system is right for you?
First, it must be determined whether the carriers and/or the material should be identified. On one hand, this depends on whether IDs can be applied to the material. Can the material be labeled or can a readable tag be affixed? If so, is there any risk that production steps may make the label illegible or damage the tag? Can the reader systems be installed in such a way that automatic identification can be achieved? Or must the identification be done manually? On the other hand, there needs to be some certainty that the handling of labeled carriers with material which is unlabeled will be done in a fail-safe manner.
A variety of tracking systems are available on the market which are suitable for a variety of applications – each with advantages and disadvantages.
Bar Code or OCR
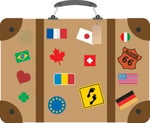
RFID
Radio Frequency ID (RFID) systems are available in different frequency ranges from low frequency (LF) to ultra-high frequency (UHF). The labels (or tags) are differentiated into passive and active categories, with the active ones requiring an external power supply. Low-frequency systems are relatively slow and require expensive tags, but the readers are cheaper and they pair well with metal. Depending on the design, UHF tags are now so cheap that they are permanently applied to the material. Due to the long read ranges, however, incorrect readings can occur (for example, through reflections) and can cause problems.
NFC
Near Field Communication (NFC) is a type of RFID that is only suitable for communication over very short distances between tag and antenna. Most smartphones have a built-in receiver for this system.
UWB
With ultra-wide band (UWB) indoor tracking – similar to GPS, the localization is performed by measuring signal propagation times to the tagged material. However, the satellites are not circling here. They are which is why they are also called anchors. The clearest distinction from the other systems is that objects can be located freely in space and do not have to reside in an area visible to their associated tracking systems. This offers a significant advantage over RFID systems. This can also translate to considerable cost savings in terms of reading devices. However, this system requires comparatively expensive, active tags.
The following table provides a rough overview of the features of some of the various material tracking systems and may serve as an introductory guide to system selection considerations. In many manufacturing environments, a combination of different identification systems is often used to meet the requirements of the area(s) and conditions under which materials are being tracked. The implementations of these systems vary widely. In some cases, applying a readable ID is not possible simply by printing adhesive labels. It also may be the case that the topology makes it difficult – or too expensive – to utilize UWB anchors.
Feature Comparison for Material Tracking Systems
* With the greatest possible variety of carrier materials
** When using passive tags where possible
Now you just have to decide on a system or a combination of systems. Based on the system you’ve chosen, you will be able to locate your materials directly after installation and St. Anthony can focus on more important matters. But manufacturing does not really become effective unless the material information is also directly available in the systems used by the manufacturing staff – or, even better, the identified material controls the production automatically. The integration and automation of processes becomes more important the more identification and IT based manufacturing systems are in use. Further information regarding integration and automation of processes can be found in SYSTEMA’s guide to digital transformation.
Be the first to comment.