Dr. Holger Brandl, on May 15, 2024, 12:32 PM
Scheduling Insights: Achieving Measurable Results with SYSTEMA APS
In a collaborative, publicly funded research project, SYSTEMA demonstrated significant opportunities for optimization by implementing our Advanced Planning & Scheduling (APS) solution in a German semiconductor frontend fab.
Initially, SYSTEMA’s data scientists conducted an exploratory data analysis to thoroughly understand the unique characteristics of the shop floor and the current state of production execution. This analysis pinpointed the epitaxy area of the production site as a critical bottleneck.
After engaging in detailed discussions with the customer’s line engineers, SYSTEMA’s data scientists integrated the insights gained into a comprehensive simulation model. This model encompassed various elements of the 4Ms – human, machine, material, and method – in production. It included considerations for staffing levels, tool characteristics, maintenance scheduling, and the requirements for setup, engineering, and qualification.
As part of the project, the following requirements for an advanced production planning solution were defined for the epitaxy area:
- tool utilization uniformity
- setup avoidance
- minimization of lot starts during shift breaks
- throughput maximization
- due date compliance
- consideration of maintenance tasks within tolerance time windows
- minimization of intralogistics
To derive the most suitable planning method, SYSTEMA data scientists studied different meta-heuristics as a baseline. In addition, SYSTEMA APS was tested as a more suitable planning approach to account for partially conflicting production targets and was found to outperform commonly used dispatching schemes (incl. the current setting at the customer’s site) in that multi-objective problem setting (see Figure 1).
Specifically, APS:
- increased area throughput by 3.6%
- improved on-time delivery by 12.3%
- minimized setup by 11.9%
- reduced intralogistics effort and setup failures
- maintained tool utilization and utilization uniformity compared to the current operation mode
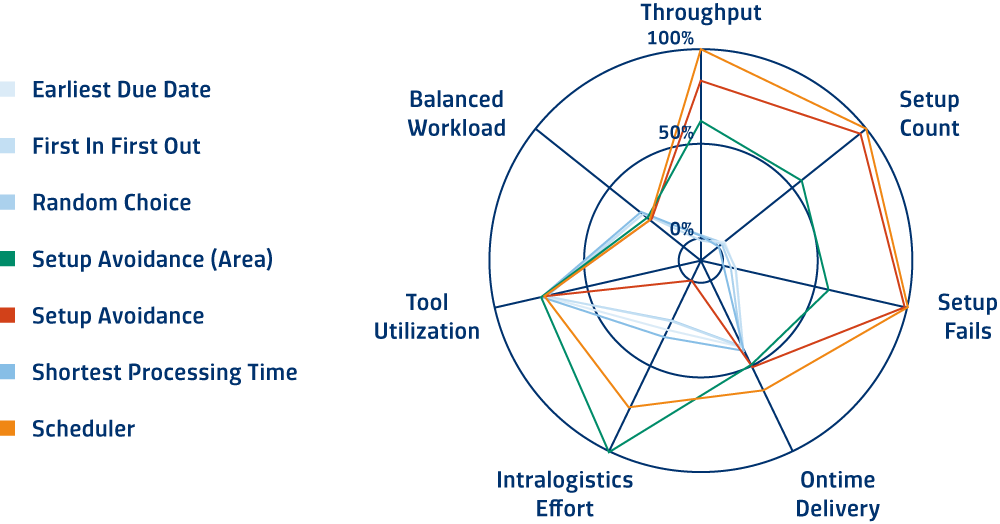
Figure 1: Results of various planning strategies (indicated by color) in terms of different production targets were derived by means of simulation. Due to multiple objectives relevant in semiconductor production planning, resulting production plans were analyzed in terms of several KPIs and normalized to allow for comparison. Intuitively, the objective is to maximize the area of the polygon (100% given as the best result and 0% as worst result for each individual KPI).
The results of our project clearly demonstrate the effectiveness of SYSTEMA’s Advanced Planning & Scheduling (APS) solution in addressing complex production challenges and enhancing operational efficiency. If your facility is facing similar challenges, or if you are interested in exploring the potential improvements our APS solution can offer, we invite you to reach out to us.
Our team of expert data scientists and engineers is ready to tailor our proven strategies to fit your unique needs, ensuring you achieve optimal production outcomes. Contact us today to begin your journey towards enhanced efficiency and productivity.
Be the first to comment.